The Ultimate Guide to ISO 9001 Training for Quality Managers & Coordinators
Being a Quality Manager or Coordinator isn’t just about inspecting products or making sure things meet the bare minimum. It’s about creating a culture that’s laser-focused on quality and continuous improvement. But let’s be real—keeping everything running smoothly while driving constant progress? It’s a challenge.
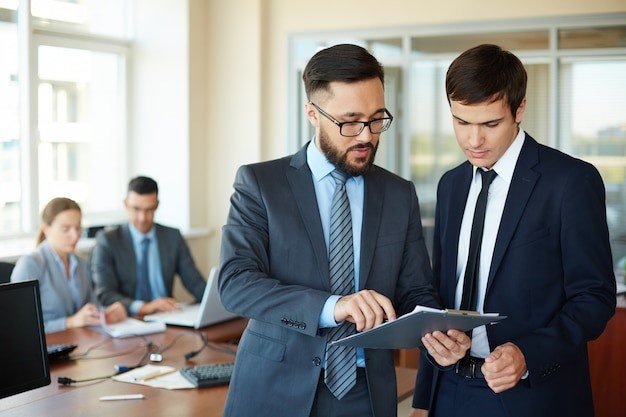
Introduction: Why ISO 9001 is Essential for Quality Managers
Being a Quality Manager or Coordinator isn’t just about inspecting products or making sure things meet the bare minimum. It’s about creating a culture that’s laser-focused on quality and continuous improvement. But let’s be real—keeping everything running smoothly while driving constant progress? It’s a challenge.
That’s where ISO 9001 comes into play. It’s not just another standard or set of regulations; it’s a proven framework that helps you streamline processes, boost customer satisfaction, and create a more efficient organization. ISO 9001 training isn’t just a checkmark on your resume—it’s a powerful tool that can transform the way you manage quality, from the ground up.
In this guide, we’ll walk through what ISO 9001 is, why it’s crucial for you as a Quality Manager, and how the right training can make a world of difference for you and your team.
What is ISO 9001? An Overview
Before we get into the specifics of training, it’s important to understand what ISO 9001 is all about. If you already know the basics, feel free to skip ahead, but if you’re new to it, let’s get on the same page.
ISO 9001 is a global standard that defines how to establish and maintain an effective Quality Management System (QMS). It’s a framework for ensuring that an organization consistently meets customer expectations and regulatory requirements while continuously improving its processes.
But here’s the thing—ISO 9001 isn’t just about compliance. It’s about adopting a mindset that prioritizes quality in everything the organization does. As a Quality Manager or Coordinator, you’re the one leading this charge, making sure quality is embedded at every level.
Why ISO 9001 Matters for You as a Quality Manager
As a Quality Manager, you’re tasked with much more than just ensuring things “work.” You’re responsible for driving improvements, enhancing customer satisfaction, and optimizing internal operations. Here’s why ISO 9001 is essential to achieving those goals:
Ø Consistency and Reliability: ISO 9001 ensures that processes are standardized, leading to consistent quality outcomes. This results in fewer mistakes, reduced rework, and happier customers.
Ø Continuous Improvement: ISO 9001 is built on the idea of ongoing improvement. It encourages you to review processes regularly, find areas for growth, and implement changes that keep the organization moving forward.
Ø Boosting Customer Confidence: Certification in ISO 9001 sends a clear message to clients that your organization is committed to quality. This boosts their trust and fosters long-term relationships.
Ø Internal Efficiency: Beyond external benefits, ISO 9001 helps streamline internal workflows, leading to a more productive and efficient team.
Core Components of ISO 9001 Training
ISO 9001 training isn’t just about learning rules—it’s about gaining the skills and knowledge to apply those rules effectively. Let’s look at some key components of the training that you’ll need to master:
1. Core Principles of ISO 9001
Understanding the core principles of ISO 9001 is critical to making it work. These principles guide every part of the QMS:
Ø Customer Focus: Everything starts with the customer. ISO 9001 ensures that the customer is at the heart of your quality management strategy.
Ø Leadership: Strong leadership is key to embedding a quality culture throughout the organization. As a Quality Manager, you’ll lead by example.
Ø Engagement of People: In ISO 9001, everyone has a role to play in maintaining quality. From top executives to line workers, each person contributes to the system.
Ø Process Approach: Quality management works best when you view your activities as interconnected processes, rather than isolated tasks. This approach leads to greater efficiency and fewer errors.
Ø Evidence-based Decision Making: Decisions should be based on data, not assumptions. ISO 9001 trains you to use performance data to make informed, effective choices.
Ø Improvement: ISO 9001 isn’t a one-time fix—it’s all about continuous, incremental improvements to processes and products.
Ø Relationship Management: Building strong relationships with stakeholders, suppliers, and customers is critical to long-term success.
2. ISO 9001 Requirements and Structure
ISO 9001 is divided into several clauses, each addressing a different part of quality management. These are the foundational concepts covered in training:
Ø Context of the Organization: This part emphasizes understanding your organization’s internal and external context—how these factors impact the QMS.
Ø Leadership and Planning: Strong leadership and well-defined planning are essential for creating a solid QMS foundation.
Ø Support and Resources: Having the right resources and infrastructure in place is vital to maintaining a QMS. This includes both human and technological resources.
Ø Operations and Processes: Learn how to design, implement, and manage processes that consistently produce high-quality outcomes.
Ø Performance Evaluation: Regular monitoring of performance data is key to measuring how well the QMS is working and identifying areas for improvement.
Ø Continuous Improvement: The ultimate goal is ongoing improvement, both in processes and in organizational practices.
3. Risk-Based Thinking
One of the key additions to ISO 9001 is the focus on risk-based thinking. This approach encourages you to proactively identify potential risks and opportunities, ensuring that the organization is always prepared for challenges.
Risk-based thinking helps you focus on what matters most, guiding decisions that reduce negative impacts and enhance the chances for success. This mindset shift ensures that you’re not just reacting to problems as they arise, but actively managing potential risks before they become issues.
How ISO 9001 Training Benefits You as a Quality Manager
So, why should you care about ISO 9001 training? Here are some major ways it benefits you and your career:
1. Enhanced Career Prospects
ISO 9001 training is a credential that employers value. It shows you have a deep understanding of quality management systems and can implement them effectively. This is a skill set that’s in demand across industries, making it a great way to open doors for career advancement.
2. Streamlined Operations
ISO 9001 helps eliminate inefficiencies by ensuring that all processes are well-defined and optimized. With training, you’ll be able to identify areas where your organization can improve, reducing waste and increasing overall efficiency.
3. Better Decision Making
With a strong understanding of ISO 9001 principles, you’ll be equipped to make data-driven decisions that lead to better quality management. Whether you're improving processes or managing resources, you’ll be able to make choices that benefit the entire organization.
4. Improved Collaboration
ISO 9001 encourages a collaborative approach, ensuring that everyone in the organization is aligned and focused on quality. By fostering this collaborative environment, you’ll build stronger teams that work together more effectively.
Practical Steps for Implementing ISO 9001
Once you've completed your training, it’s time to put your knowledge into action. Here’s how to implement ISO 9001 in your organization:
1.Get Executive Buy-In: For any ISO 9001 initiative to succeed, it’s critical to have support from top management. Make sure they understand the benefits and are committed to the process.
2.Train Your Team: ISO 9001 isn’t just for you—it’s for the entire organization. Ensure everyone is trained on their role in the QMS, from top leadership to the shop floor.
3.Document Your Processes: ISO 9001 requires detailed documentation of processes. This creates a clear roadmap for how things should be done and ensures consistency.
4.Measure Performance: Use Key Performance Indicators (KPIs) to track the effectiveness of the QMS. Regular evaluations allow you to make adjustments and keep improving.
5.Focus on Continuous Improvement: ISO 9001 is a never-ending journey. Use regular audits, feedback, and data analysis to continuously improve your systems and processes.
Conclusion: Why ISO 9001 Training is an Investment in Success
ISO 9001 isn’t just another certification. It’s a mindset that shapes the culture of quality within your organization. As a Quality Manager or Coordinator, investing in ISO 9001 training is a strategic decision that will not only improve your personal expertise but also enhance your team’s ability to deliver outstanding results.
By learning the principles, mastering the requirements, and actively implementing them, you’re not just meeting a standard—you’re setting your organization up for long-term success and continuous improvement.
Are you ready to take the next step? With ISO 9001 training, you’ll have the tools to lead your organization toward a future defined by quality, efficiency, and ongoing success.
What's Your Reaction?

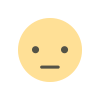

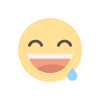


